Made in JAPANの信頼をMade by TOYOTAで実現するために
ハイラックスは日本から始まり、北米、オーストラリアそしてタイと、世界の地域で優れた信頼性、耐久性、オフロード機動性で長年にわたり高い評価をいただいてきました。
一方、インドネシアやフィリピンでは、1976年から積載重量1トンクラスのピックアップトラックのTUV(TOYOTA Utility Vehicle)の現地生産が開始されました。インドネシアではキジャンというネーミングです。1990年以降、ピックアップトラックから派生した多人数乗用車モデルが国民車として名声を博すまでに至りました。どちらもラダーフレームにボデーを搭載したボデー構造だったため、ハイラックスとキジャンのプラットフォームを統一できないか、とその頃から幾度も議論がされた経緯がありました。
そんな中、7代目ハイラックスの企画は1トンピックアップトラックでありながら、キジャンをベースとしたMPV、サーフをベースとしたSUVなど、5タイプのボデーのプラットフォームを統一して開発するIMV(Innovative International Multipurpose Vehicle)プロジェクトとして始まりました。しかし、インドネシアの国民車キジャンは、生産コストを抑えながら、荷物も人もたくさん運べるクルマにしなければならない。一方、規制が厳しい欧州向けがあるハイラックスはワークユースだけでなく、乗用車替わりの使い方もあるので、乗り心地や居住性をよくしなければなりません。それにはコストがかかります。こうした相反するものを、当時の開発責任者はなんとか一緒にする方法を模索し続けてきましたが、なかなか相容れることができませんでした。しかし1997年のアジア通貨危機を契機にアジア圏での海外生産事業のあり方について真剣に検討がされました。即ち、為替リスクの回避です。一方、北米市場をみたとき、FordのF150などBig3のピックアップ達が非常にリーズナブルな価格で毎月数万台と乗用車より多く販売されている事実をみて、量をまとめて安価なクルマ作りをしよう、となったのです。ハイラックスとキジャンを統一することでスケールメリットを出して、現地生産でお客様にリーズナブルな価格でクルマをお届けしたい。これがIMVプロジェクトの原点、と私は認識しています。98~2000年の間、役員方が中心となり粘り強くコンセプトを練られたのです。先輩方のチャレンジ精神には今でも頭が下がります。
私は1996年から製品企画部に配属となり2000年当時は主査として北米生産プロジェクトのセコイヤ開発に従事していました。その年の秋の立ち上がりの準備で米国インディアナ工場に長期出張していた時のことです。「製品企画部内でIMVの成立検討が開始された模様だ」と同僚が伝えてきました。ハイラックスとキジャンのプラットフォームを統一して複数ボデーを同時開発、しかも日本での生産はなく、アジア各国、南米、南アフリカで現地生産するらしい、と。
しかし、その時の私は、セコイヤの立ち上げで頭が一杯。IMVの噂なんて右の耳から左の耳へ。まさか、その後IMV担当になるとは、夢にも思いませんでした。2000年秋にセコイヤが無事立ち上がり、ホッとする間もなく、2001年より新興国向けモデルの担当になりました。U-IMV(ダイハツとの共同開発プロジェクトでIMVミニバンの小型版開発)でした。
この企画にトヨタ代表として参画、約1年間、ダイハツと一緒に企画を練り上げました。そして、意匠開発をこれから進めようとした矢先、2001年の12月末でした。
上司から「来年からIMVプロジェクトを担当してもらう」と告げられたのです。
これは大変なことになったと思いましたが、今思えばセコイヤ開発でラダーフレームのプラットフォーム設計のカンやコツ、そしてU-IMVプロジェクト参画でインドネシア等初めて新興国市場を経験できたことが、その後のIMV製品企画でとても役に立ちました。
多次元カレンダーで見える化を進める
2002年1月、IMVとは何か?と勉強する間もなく、実開発の大波にのみこまれました。
IMVプロジェクトの頭だしは2004年8月のタイのハイラックス、インドネシアのキジャンのフルモデルチェンジです。与えられた時間はわずか2年8カ月。ピックアップのハイラックスで3車型、SUVのフォーチュナー、ミニバンの同時開発提案の承認を得る、意匠の承認を得る、という大仕事を年内でやり遂げる使命を帯びたのです。新米チーフエンジニアが全て仕切れた訳ではありません。
実は98年から技術部門と営業部門の各専務がリーダーで、開発をはじめ生産、調達、販売の事業軸も絡めてIMVプロジェクトの検討が進められていたのです。ハイラックスとキジャンのプラットフォームを統一、5タイプのボデーを同時に開発し、日本での生産はなく、アジア、南米、南アフリカでのグローバル生産にて、主要5カ国の工場でほぼ半年以内にそれぞれを立ち上げ、部品も現地調達率100%を目標にする。IMV(Innovative International Multipurpose Vehicle)プロジェクトと呼ばれ、「Made in Japan」や「Made in Thailand」ではなく、「Made by Toyota」として世界へ供給する、壮大で革新的なプロジェクトです。
こんなIMVプロジェクトの青写真が2000年後半には既にできていたのです。
私のIMV参画以前から生技、製造など各機能があのIMVの青写真を基に色々な準備や検討を進めてくれていたのです。お陰で各国での生産準備から遡って決まる設計図面での日程を基に、技術部側は評価も含めた細部の日程まで落とし込みがなされていました。開発側には非常に厳しい日程でしたが。青写真のお陰で、製品企画はゼロからのスタートでない点がIMV初心者の私には大助かりでした。最初から調達、生産技術、製造、営業が一体となって具体的な意見を出し合うことができました。生技と開発の間では日々厳しい議論の応酬もあったものの、各国で異なるモデルが順番に立ち上がってゆく青写真の高い志を、海外の事業体、サプライヤーさん達とも共有できていた点が、当初予定通り2004年8月の立ち上がりを迎えられた要因の一つと思います。当時は海外にR&D組織はありませんでした。TMC設計者にとっては、多くの新興国を股にかけた難しい仕事だったはずですが、青写真の持つ意味をよく理解しモチベーションを高くもって設計に集中できたことが、私には頼もしく見えました。
実開発のスタート時点でコピー生準と原価企画がIMVを物語る大事な要素でした。
コピー生準とは先頭国のタイ、インドネシアの工場で使う型をしっかり作ること。これをコピーして南アフリカ、アルゼンチンへ拡げていく。だから最初の型をいかに高い精度で作るかがとても大事でした。設計陣はいかに設計図面の出図日程を遵守するか、でした。
原価企画も大変でした。私が以前に担当していたセコイヤは日本円と米ドルで計算しましたが、IMVではタイバーツ、インドネシアルピー、アルゼンチンペソ、南アフリカランドなど、10種類以上の通貨で計算しなければなりません。
原価企画は開発提案という大きな節目までに厳しい原価目標を達成する作戦を揃えないといけません。設計者はコピー生準や原価企画を推進するためのカレンダーを、個々の部品毎に作戦付きで持つことになります。設計は実験や生技の協力の元、いつまでに何をするかを可視化しました。更に車型、エンジン型式、グレード、生産国等が考える切り口が多いので、部品毎に高度な見える化の工夫も迫られます。すると多くの要件を織り込んだ複雑なカレンダーになってゆきます。正に、多次元カレンダーです。設計のみならず、評価部署もこんなカレンダーを作りました。これを作らないと自分達の仕事の全貌が掴めないのです。設計、実験のフロアには進捗OK/NGが一目で判るボードが何枚も立て掛けられていました。全関係部署が共有できるのです。
IMVプロジェクトの複雑さ故に私は自分の立ち位置を見失いそうな時、IMVチームはいつもプロジェクト進捗を見える化してくれていたことが私にとって大きな支えでした。
2002年後半になると試験車が出来上がり、走行試験等を繰り返し開発が進みました。
試験車が走り出すと、仕事が動き出したなぁ、という実感が湧いてきました。
タイTMTの熱意とリーダーの決断
時は2003年10月、タイの工場(トヨタ・モーター・タイランド、以下TMT)での立ち上げ10カ月前となりました。開発から生産にハンドオーバーする時期です。即ち、開発はほぼ完了していなければいけない時です。開発完了できているかどうか技術部総出で確認作業に入った所、予期せぬ不具合が多く出てきました。ここからの設計変更はかなりきついのです。私達は大会議(号試移行会議)の事前でその状況を関係者で共有し、号試開始を1カ月程度遅らすことも選択肢で持ちました。TMCのそんな雰囲気がTMTにも伝わった様でした。こんなIMV準備状況を心配されていた当時のアジア本部長の豊田章男専務がTMTを視察、そこでTMTの人達は言いました。『この程度の設計変更だったら1カ月遅らさないで欲しい、自分たちが絶対やり遂げるから、予定通りに進行しましょう。大丈夫です』と。彼らはIMVの生産拠点としてのプライドがあり、このプロジェクトにかける熱い思いが専務に伝わったのでしょう。その後の号試移行会議で、私が全体の進捗状況を説明して懸案の今後の進め方について号試を遅らせたい旨を言おうとした時でした。
豊田章男専務が「予定通り進めてください。何かあればアジア本部長の私が全ての責任を持ちます。」と会議を締められたのです。2003年11月のこと、今も忘れられません。
これで収束すれば良かったのですが、実はもうひとつ、ヤマがありました。
2004年1月にTMTで関係役員による総点検の場がありました。またまた設計変更をしなければならない不具合がたくさん見つかりました。1月のバンコク、とても暑いTMT工場の建屋の中で私は冷や汗びっしょりでした。生技、製造そしてサプライヤーさんの協力を得て技術部総力を挙げて事態の解決へ向けて挑むことになりました。対策を織り込んだクルマを田原の悪路テストコースで耐久走行試験をしなければいけません。当時は耐久走行距離は15,000km走破が基本。通常だと1カ月半から2カ月かかります。しかし号試日程に影響させず全ての宿題をやり遂げるには耐久走行試験は正味1カ月で終わらせるしかない。すると評価部門のテストドライバーたちは、「徹夜で走らせれば間に合うから大丈夫だ」と言ってくれ、昼夜交代しながら1カ月で走ってくれました。ここでまた何か不具合が出たら、私は絶体絶命の大ピンチ。しかし、4月末には不具合はすべて解消され、8月の立ち上がりに向け予定通りに号試が進行できました。胸を撫で下ろしました。最後に帳尻があった訳です。8月のタイでの発表を迎えることができました。ただここで終わりではありません。
一息つく暇もなく更に高い性能を目指して
2004年8月、タイ、インドネシアと販売が開始されましたが、翌年に欧州、オーストラリアそして中東など世界各国への輸出が始まります。開発難度の高い仕事が1年後に控えていたのです。例えば、使用環境ではタイであれば最高気温は35℃くらいですが中東は45℃で、砂漠走行ではエンジンの負荷が増え冷却性など厳しい条件になります。欧州向けエンジンは当時の排気規制Euro4の適合開発が追加になったりして8月以降も依然としてやるべきことがたくさんありました。一息つく暇もありませんでした。
ここで、技術ノウハウの織り込みの観点で言うと、ハイラックスとしては7代目になりますので、過去にハイラックスで培ってきたノウハウをしっかり注ぎ込み、もっと良いハイラックスを目指して作ってきました。エンジンもランドクルーザー系のプラドや70系と同じエンジンを搭載するグレードも用意しました。するとユーザーから新たな注文が出てきました。私としては先代モデルのハイラックスより、性能の良いハイラックスを作った、と自負していましたが、ユーザーは先代ハイラックスではなく、ランドクルーザー系のモデルと比べるようになっていたのです。例えば、鉱山での作業車としては、ランドクルーザー70のピックアップと比較されました。もちろん乗り心地はハイラックスのほうが良いのですが、不整地路面で長期間使用してきたときの耐久性で差が露見します。
私をはじめ、多くのエンジニア達は2004年の立ち上がり後も市場から様々なことを学びました。
ハイラックスは厳しい社内基準を十分クリアできる設計仕様で仕立てましたが、先代及び以前のハイラックスには、その基準をはるかに超える耐久性を有していた部位もあったのです。それはハイラックスを代々乗り続けて頂いているお客様の期待を裏切ることにもなり得るのです。過去から蓄積されたノウハウをしっかり活かして開発したつもりが、市場(お客様)の不変な点と変化点を読むことは大変難しいものだと痛感しました。
またハイラックスは日本で言えば商用車の感覚が強いので、マニュアルエアコンでよいと思うのですが、現地では乗用車感覚で乗られるので、オートエアコン、パワーウインドウを強く要望され、最初は理解しにくい点もありました。コストを考えず上質なクルマを作ろうとすれば簡単なことですが、容易には踏み切れません。幾度も設計部門とは安価な設計について、営業部門とは価格の折衝を幾度となくしました。やはり製品企画の仕事とは、市場、ユーザーの相場観を持つことがとても大事だと改めて思いました。私達は現地へ行って現地の人達と意見交換しながら、相場観を持つ努力をしてきたつもりです。導入地域毎に違う相場観が持てた、と実感を得るのに正直言って何年もかかりました。
サイズを大きくして人も荷物も快適に移動できるように
7代目ハイラックスは、国内販売がなかったため、日本の車幅制約1,700mmにとらわれることなく設計ができました。人間工学に基づき、車内の居住性を考え、営業/設計/実験などの各部門のみなさんで意見を出し合いながら決めました。ただ荷物は物を言わないのでデッキサイズはどうしようかと。そこでTMTに相談した所、果物運搬用のバスケットのサイズに規格があるので「これが何個積めるか」で決めてはどうか、と提案をもらいました。これはいい案だと思い、競合モデルよりひとつでも多くのバスケットを積める様にしました。キャビンとデッキでボデーサイズがほぼ決まったところで、ホイールベースは少しでも最小回転半径を小さくしたいので、ミリ単位で縮める検討に入りました。回転半径を決める際にもTMTのスタッフが、先代モデルのバンパーにウレタンをつけて、7代目ハイラックス検討の車幅を模擬したクルマを作って、バンコクの市街地をいろんな条件で走ってくれました。渋滞、狭い道路などを走って駐車して、どのくらいの車幅だったら、タイで受け入れられるかを確かめてくれました。ピックアップトラックが多く集まるバンコクの朝市でも確かめてくれました。こうしたシンプルですが地道な準備のおかげでユーザーからは、7代目は大きな進化をしたと高い評価をいただきました。結局、7代目ハイラックスは先代より車幅を60mm拡幅しましたが、最小回転半径はステアリング系の改良などにより先代より0.2m改善されました。
ただ発売してから時が経つと、各国で新たな課題が提起されました。タイでは家族で乗用車替わりに使うお客様が多いですが、オーストラリアはパークレンジャーなどプロフェッショナルユースで多く使われます。まるでオフロードのテストコースのような悪路を日常的に走ります。一つの設計仕様でどちらの用途にも対応させるのはとても困難です。
またオーストラリアではトーイング能力の容量不足を指摘されました。先代モデルと同じトーイング能力は確保していたのですが、折角のエンジンのパワー、トルクが大きくなったのだから、もっとトーイング能力を上げなければと。確かにタイでは牽引する風土がありません。正直言ってオーストラリア市場を甘く見ていた、と言うしかありませんでした。
世界中のユーザーの声もできるだけ取り入れ、2011年にマイナーチェンジを行いました。2008年に続く2回目の大規模マイナーチェンジでした。ちなみに2008年のマイナーチェンジではタイ向けのCキャブにアクセスドアを採用しました。この開発はTMAP-EMの若いエンジニア達が主力でした。TMAP-EMの自立化に向けよく頑張ってくれました。2011年のマイナーチェンジでは意匠改良、走行性能向上など2004年以降に市場で学んだ宿題などやるべきことはやれた、と思います。ある意味、自信作でした。ただ、やれなかったのは、オーストラリアなど南半球のお客様にも充分応えられるタフさです。これは8代目ハイラックスに託すことになりました。
ハイラックスはもっと進化する
ハイラックスは誕生以来ラダーフレームを採用しています。一方、クルマはずっと以前からモノコックボデーが一般的です。昨今、環境対応、低燃費化の観点で車両質量はモノコック構造の方が軽くなるからトラックにも、という論調があります。が、ハイラックスなど未舗装路を日常的に走り続ける使用条件で耐久性、信頼性を確保するにはモノコックボデーでも結局、それ相当な質量増が必要、と思います。ラダーフレーム構造のボデーとは?
衝突の際にはフレームが潰れたり曲がったりの変形をさせて衝突エネルギーを吸収、路面からの衝撃にはサスペンションがしなやかに吸収、そのサスペンションが取り付くフレームは剛性がしっかり確保された上で、タイヤとサスペンションが路面の凹凸をいなしながら動くための土台の役目を果たします。
リヤのリーフスプリングは上下入力の緩衝装置、という見方は正しいですが、実はハイラックスのリーフスプリング設計にはリーフが1枚ずつ擦れる抵抗やさらに三次元的によじれることで凹凸のある不整地路面でも左右のタイヤができるだけ接地できるノウハウが込められています。単なる上下の緩衝装置以上の機能がある訳です。地味なリーフスプリングタイプのリアサスペンションですが、トヨタのオフロード性能のDNAが注入されているのです。私はラダーフレームやリーフスプリングは、信頼性、耐久性は当然、走行性能、静粛性などまだまだ進化できる余地がある、と思っています。そして将来のハイラックスは、8代目ハイラックスのタフさに更に磨きがかかり、もっと世界へ飛躍してゆくだろう、と願っています。
最後に私にとってIMVとは?
少なくともIMV第1弾の2004年タイ/インドネシア立ち上がりの時までは、私は多くの皆さんに引っ張っていただいた、という感が強くあります。チーフエンジニアらしくありませんね。
IMVが成功、と当時各方面から高い評価をいただきました。それはオールトヨタの結束力、そして、私が開発に参画する3年前から、ハイラックスとキジャンのプラットフォームを統一して同時開発するとか、世界同時立ち上がりなど調達、生産、販売の事業面でのプロジェクトの青写真がしっかりできていたことが、IMVプロジェクトの成功のキーと思います。私はIMVプロジェクトという壮大な仕事で、新車開発の所でのリーダーなのです。
私がチーフエンジニアらしく仕事ができた、と実感するのは2004年から中嶋さんにバトンタッチする2011年の夏までの期間です。右肩上がりの販売を維持できました。リーマンショックやタイ大洪水など瞬間的に逆風に見舞われたことはありましたが、世界経済、各国の政情、総じて安定して良い時期でした。私は本当に良い星の下で仕事ができた、ということです。
そして、世界各国で多くの友人を持つことができました。何にも代えがたい財産です。
- 7代目ハイラックス開発責任者
- 細川 薫(ホソカワ カオル)
- 昭和54年4月
- トヨタ自動車工業株式会社入社
- 平成11年1月
- トヨタ第3開発センター、主査(初代セコイア担当)
- 平成13年3月
- トヨタ第3開発センター、チーフエンジニア(U-IMV担当 : ダイハツとの共同開発)
- 平成14年1月
- トヨタ第3開発センター、チーフエンジニア(IMV担当、ハイラックス含む)
- 平成23年9月
- 製品企画部、地域担当部長(欧州/日本担当)
- 平成24年4月
- 住友ゴム工業株式会社へ出向、タイヤ技術開発本部理事
- 平成26年3月
- 住友ゴム工業(株)出向終了と同時にトヨタ自動車(株)定年退社
- 平成28年5月
- ダイハツ工業株式会社に技術アドバイザーとして就任、現在に至る。
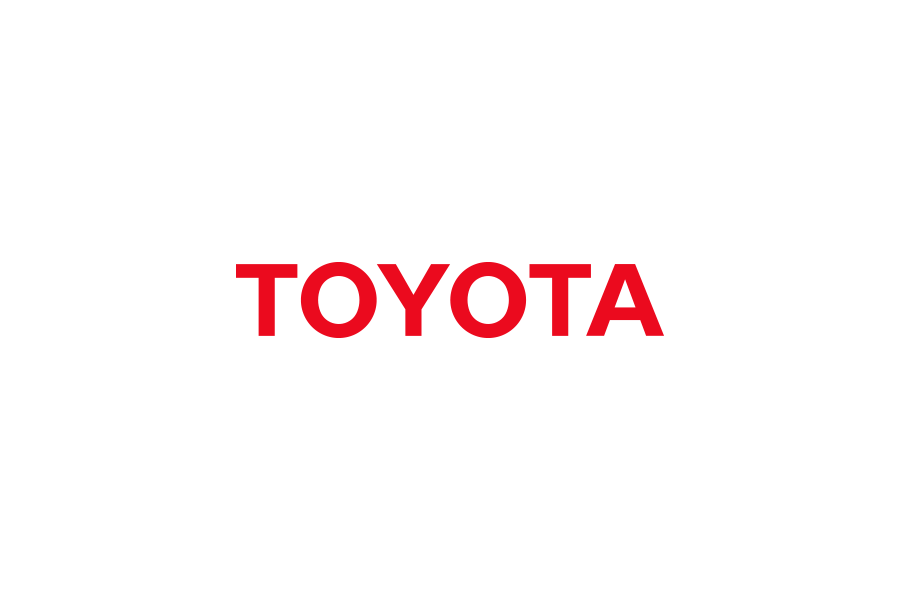